CNC Machining/Milling
CNC Milling is a process that consists of a variety of precision cutting tools and rotary cutters to make a component by removing the raw material. Our machines are installed to high specifications that include high pressure coolant, through spindle coolant, thread milling and the facility for wireless data transfer from our systems. We have the ability of doing on and offline programming using Edge/CAM and Solid Works.
CNC machining allows us to be efficient, highly accurate and economical; improving our quality and turnaround time. Our engineers program the equipment to enhance cutting time, surface finish and tolerance to meet your specifications. While using their expertise to measure the geometric and positional parameters between milled features and gears or splines.
Here at Newmont our Milling machines enable the manufacture of instrument gear boxes, motor plates, cover plates and housings. We regularly machine components from a wide range of high grade aerospace materials such as Aluminium, Brass and Stainless Steel to name a few. Currently our most challenging parts are 4-Axis Vertical work on universal joints, yokes and splined couplings. The production of prismatic components is supported by our three coordinate measuring machines (CMM) in our Inspection department.
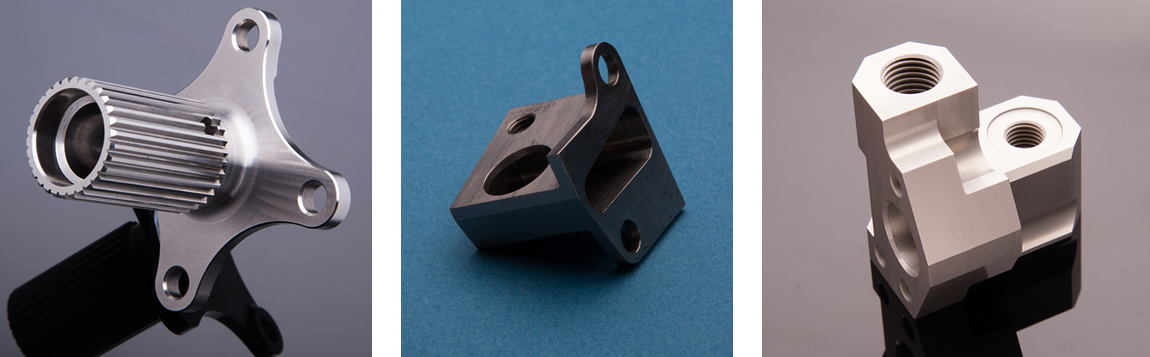
Turning
Turning (like CNC Milling) is a form of machining to create rotational parts by cutting away unwanted material using a turning machine or lathe. Newmont offer CNC turned parts from high grade materials and customer specific composite materials (e.g. carbon fibre) to machine.
We have an extensive Turning section including 11 CNC Lathes offering the ability to manufacture a wide range of high quality parts. Most of our work on these machines are for the aerospace industry; couplings, splined shafts,yokes, cross shafts, hubs, reaction plates, lead screws, quill shafts, brake plates, spur gears and bevel gears.
Our HAAS TL-25 SE with its twin-spindle configuration and ample power is best suited for any heavy machining turning operation; our three Okuma lathes have live tooling and are capable of continuous precision finishing. The CT1118 platen lathe has a low power wrap round pneumatic collet chuck for holding thin and delicate parts – facilitating the production of thin discs and brake plates. Using Citizen sliding head and Hardinge sub spindle machines we have the capacity of machining 5 – 42 mm bars and parts of up to 400mm diameter.
With our wide range of machines, the different variations of cutting feed, cutting speed, spindle speed, axial depth of cut and radial depth of cut allow us to machine parts from small pinions to complex yokes.
Take a look at the primary machinery we use in our Milling section: